1.
Chemische Gasphasenabscheidung (CVD): Als Kohlenstoff-Quellgase werden in der Regel Kohlenwasserstoffe wie Ethylen und Methan verwendet, während für den Katalysator in der Regel Metallkatalysatoren wie Eisen, Nickel, Kobalt usw. gewählt werden. Das abzuscheidende Substrat (z. B. eine Siliziumscheibe, eine Glasscheibe usw.) wird in eine Reaktionskammer gelegt, um sicherzustellen, dass die Substratoberfläche sauber und eben ist. Die Reaktionskammer wird auf eine geeignete Temperatur aufgeheizt und dann auf ein bestimmtes Vakuumniveau abgesaugt, um die Reinheit und Stabilität der Gase während des Reaktionsprozesses zu gewährleisten. Das Gas der Kohlenstoffquelle und das Katalysatorgas werden über ein Gaszufuhrsystem in die Reaktionskammer eingeleitet, um den Gasdurchsatz und das Durchflussvolumen zu steuern. Das Gas der Kohlenstoffquelle dissoziiert an der Katalysatoroberfläche und erzeugt Kohlenstoffatome, die sich anschließend auf der Substratoberfläche ablagern und Kohlenstoffnanoröhren bilden. Die Wachstumszeit der Kohlenstoff-Nanoröhren wird gesteuert und reicht in der Regel von Minuten bis Stunden, um die Länge und Dichte der Nanoröhren zu kontrollieren. Längeres Wachstum führt zu längeren und dichteren Kohlenstoff-Nanoröhren. Am Ende des Wachstums wird die Zufuhr von Kohlenstoffquelle und Katalysatorgas gestoppt und die Reaktionskammer auf Raumtemperatur abgekühlt. Am Ende der Reaktion wird das Restgas in der Reaktionskammer durch Zufuhr eines Inertgases wie Stickstoff oder Argon entfernt.
2. Beschichtungs-Methode: Die Kohlenstoffnanoröhrchen-Suspension wird durch Schleudern, Sprühen, Streichen oder Rollen auf die Substratoberfläche aufgebracht. Während des Beschichtungsprozesses können Parameter wie die Beschichtungsgeschwindigkeit und die Rotationsgeschwindigkeit des Beschichtungskopfes gesteuert werden, um die Dicke und Gleichmäßigkeit des Films zu kontrollieren. Nach dem Beschichten wird die Beschichtung in einem belüfteten Bereich oder auf einer beheizten Bank platziert, um die Verdunstung des Lösungsmittels einzuleiten. Nachdem das Lösungsmittel vollständig verdampft ist, wird getrocknet, um einen gleichmäßigen Kohlenstoff-Nanoröhren-Film zu bilden. Optional wird der Kohlenstoffnanoröhrenfilm einer Wärmebehandlung unterzogen, um die Kristallinität und die mechanischen Eigenschaften des Films zu verbessern. Die Wärmebehandlungsbedingungen können je nach Bedarf angepasst werden und werden in der Regel unter einer Inertgasatmosphäre durchgeführt.
3. Filtration: Zu den üblicherweise verwendeten Filtermembranen gehören Membranen aus Polycarbonat (PC), Polyester (PET) und Polyamid (Nylon), wobei die Porengröße in der Regel auf der Grundlage der gewünschten Filmdicke und Durchlässigkeit ausgewählt wird. Die Suspension der Kohlenstoffnanoröhrchen wird durch Vakuum oder Druck auf die Filtermembran filtriert. Die Filtration kann mit Geräten wie Vakuumfiltrationstrichtern oder Membranfiltern durchgeführt werden.
4. Abziehverfahren: Zu den üblichen Abziehverfahren gehört das mechanische Abziehen, bei dem die Kohlenstoffnanoröhrenschicht direkt vom Substrat mit Abziehwerkzeugen (z. B., (z. B. Bänder, Schaber usw.) direkt vom Substrat abgezogen wird; chemisches Strippen, bei dem der gewachsene Kohlenstoff-Nanoröhrenfilm in ein geeignetes Lösungsmittel oder eine Lösung gegeben wird, so dass die Bindung zwischen dem Film und dem Substrat beschädigt wird, um das Strippen zu realisieren; und thermisches Strippen, bei dem das Substrat oder der Film erhitzt wird, so dass es sich thermisch ausdehnt oder zusammenzieht, um die Bindung zwischen dem Substrat und dem Film zu zerstören, um das Strippen zu realisieren; und thermisches Strippen, bei dem das Substrat oder der Film erhitzt wird, so dass es sich thermisch ausdehnt oder zusammenzieht, um die Bindung zwischen dem Substrat und dem Film zu zerstören, um das Strippen zu realisieren. Beim thermischen Strippen wird das Substrat oder der Film erhitzt, so dass es sich thermisch ausdehnt und zusammenzieht, wodurch die Verbindung zwischen Substrat und Film zerstört wird.
5.3.3 Fallstudie: Mit Kohlenstoffnanoröhrchen verstärkte Umkehrosmosemembranen
Eine einzigartige Anwendung von Kohlenstoff-Nanoröhrchen, zusätzlich zu den funktionalen Anwendungen, die anderen Arten von Filtrationsmembranen ähneln, sind Umkehrosmosemembranen. Diese Membrantrenntechnologie ist in der Lage, Verunreinigungen, Ionen, Mikroorganismen usw. aus dem Wasser abzutrennen, was in den Bereichen Trinkwasser, industrielle Abwasserbehandlung und Meerwasserentsalzung weit verbreitet ist. Die Umkehrosmose-Membran hat jedoch das Problem des geringen Durchflusses und der niedrigen Verarbeitungseffizienz. Um dieses Problem zu lösen, haben Wissenschaftler Kohlenstoffnanoröhren in Umkehrosmosemembranen eingesetzt. Kohlenstoff-Nanoröhrchen haben hervorragende Eigenschaften wie eine hohe spezifische Oberfläche, hohe Festigkeit, hohe Leitfähigkeit usw., die eine Art Protonenleiterkanal in der Umkehrosmosemembran bilden und den Durchfluss erhöhen können. Gleichzeitig können Kohlenstoffnanoröhren auch Ionen, Mikroorganismen und andere Verunreinigungen im Wasser adsorbieren, was die Wasserreinigungseffizienz und die Lebensdauer der Umkehrosmosemembran effektiv verbessern kann. Derzeit ist die Umkehrosmose-Membran auf der Grundlage von Kohlenstoff-Nanoröhrchen in den kommerziellen Einsatz gebracht worden, im Bereich der Trinkwasser-, Meerwasser-Entsalzung, und anderen Bereichen, um wichtige Ergebnisse zu erzielen. In Zukunft werden die Forschung und die Herstellungstechnologie von Kohlenstoff-Nanoröhren-Materialien weiterentwickelt, und der Durchfluss und die Verarbeitungseffizienz von Umkehrosmosemembranen werden kontinuierlich verbessert.
Tabelle 2 Vergleich der Eigenschaften von TiO2-Nanoröhrchen, GO und CNT
Eigenschaften | Titandioxid (TiO2)-Nanoröhrchen-Membranen | Graphen-Oxid (GO) Membranen | Kohlenstoff-Nanoröhrchen (CNT)-Membranen |
Struktur des Materials | Titanoxid-Nanoröhrchen | Graphenoxid mit sauerstoffhaltigen funktionellen Gruppen | Kohlenstoff-Nanoröhrchen |
Herstellung Methode | Lösungsverfahren Aufdampfverfahren Elektrochemisches Verfahren | Beschichtungsmethode Chemische Gasphasenabscheidung Hydrothermale Methode | Chemische Abscheidung aus der Gasphase Beschichtungsmethode Filtrationsmethode |
Anwendungsgebiete | Photokatalyse Photovoltaische Geräte Wasser- und Luftreinigung | Wasseraufbereitung Luftreinigung Molekulare Trennung Biomedizin | Wasseraufbereitung Umkehrosmose-Membranen Molekulare Trennung Biomedizin |
Vorteile | Große Oberfläche Besondere photovoltaische Eigenschaften Photokatalytische Aktivität | Viele sauerstoffhaltige funktionelle Gruppen Hohe Oberflächenaktivität Molekulare Selektivität | Hohe Festigkeit Hohe Leitfähigkeit Hohe spezifische Oberfläche Regelbare Leistung |
Nachteile | Aufwändiger Herstellungsprozess und hohe Kosten | Anfällig für strukturelle Defekte und schlechte Stabilität während des Präparationsprozesses | Komplexer Präparationsprozess Hohe Anforderungen an die Prozesskontrolle |
Anwendungen | Photokatalytische Wasseraufbereitung Luftreinigung Herstellung von photovoltaischen Geräten | Wasseraufbereitung Molekulare Trennung Biomedizinische Anwendungen | Umkehrosmose-Membranen Molekulare Trennung Biomedizinische Anwendungen |
6 Membranen auf der Basis von metallorganischen Gerüsten (MOF)
6.1 Was sind MOF-Membranen?
Ein
metallorganisches Gerüst (MOF) ist ein Koordinationspolymer, das durch Selbstorganisation von mehrzähnigen organischen Liganden, die Sauerstoff, Stickstoff usw. enthalten, mit Übergangsmetallionen hergestellt wird. Es besteht aus anorganischen Metallzentren und verbrückenden organischen Liganden, die durch Selbstorganisation miteinander verbunden sind und ein kristallines poröses Material mit einer periodischen Netzwerkstruktur bilden. Als organisch-anorganisches Hybridmaterial haben MOF sowohl die Steifigkeit anorganischer Materialien als auch die Flexibilität organischer Materialien.
Die rückgratartigen Strukturen in verschiedenen Dimensionen werden hauptsächlich durch die Koordination zwischen organischen Liganden und Metallionen sowie durch Wasserstoffbrückenbindungen bestimmt. Während des Syntheseprozesses besetzen Restreaktanten und kleine Lösungsmittelmoleküle die Poren der Skelettstruktur, während die Entfernung kleiner Moleküle durch Aktivierungsbehandlung eine dauerhafte Porenstruktur hinterlassen kann. Die Größe und Struktur der Poren kann durch Änderung der Struktur der organischen Liganden und der Art der Metallionen im synthetisierten Ausgangsmaterial verändert werden, um die spezifische Oberfläche und Porosität für verschiedene Anwendungen zu steuern. Gegenwärtig können metallorganische Skelettmaterialien in Verbindung mit stickstoffhaltigen heterozyklischen organischen neutralen Liganden oder mit carboxylhaltigen organischen anionischen Liganden in großen Mengen synthetisiert werden, was ein großes Potenzial für die Entwicklung und Anwendung in der modernen Materialforschung darstellt.
6.2 Wie man MOF-Membranen herstellt
1. In-situ-Synthesemethode: Aufgrund der besonderen Oberflächeneigenschaften des Trägers wird dieser direkt in das Synthesesystem eingebracht, und unter bestimmten Bedingungen kommen die Oberfläche des Trägers und die filmbildende Nacht direkt in Kontakt und reagieren, um eine kontinuierliche Membran herzustellen. Die In-situ-Synthesemethode ist einfach und leicht zu bedienen, leicht zu realisieren großtechnische Produktion, aber es ist schwierig, kontinuierliche MOF-Membran vorzubereiten, weil die chemischen Eigenschaften zwischen MOF-Materialien und Träger sind mehr unterschiedlich, die Rate der Kristallkeimbildung ist reduziert, was zu einer geringen Dichte der heterogenen Keimbildung von MOF-Kristallen auf der Oberfläche des Trägers, und schlechte Bindung zwischen der Membran und dem Träger.
2. Kristallkeim sekundäres Wachstum Methode: zunächst die hydrothermale Methode, um die Kristallkeim auf dem Substrat wachsen, und dann nach dem Prozess der Kristallkeimbildung, Membranschicht Wachstum, das Material sekundäre Wachstum für dichte Membran. Schließlich ist die poröse Substratoberfläche Kristallarten nach hoher Temperatur, die Kondensationsreaktion zwischen den Gruppen, und Zeolith-Körner kombiniert, um kovalente Bindungen zu bilden. Allerdings ist die Methode etwas eingeschränkt, weil die Filtermembran nicht hohen Temperaturen standhält.
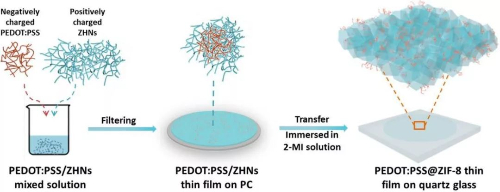
Abb. 10 Schematische Darstellung der Synthese eines MOF-Films: PSS@ZIF-8-Film
6.3 Spezialisierte Anwendung zur Entfernung von Schwermetallen
Zusätzlich zu den funktionellen Anwendungen, die denen anderer Filtermembranen ähneln, können MOF-Membranen auch zur Behandlung von Schwermetallionen eingesetzt werden. MOF-Membranen haben eine hochgradig geordnete poröse Struktur, die von Metallionen und organischen Liganden durch chemische Ligandenbindungen gebildet wird. Diese poröse Struktur hat einen einstellbaren Porendurchmesser und eine einstellbare Porengröße und bietet viele Adsorptionsstellen und Kanäle, die für die Adsorption und Einbettung von Schwermetallionen günstig sind. Dies ermöglicht den Einsatz von MOF-Filmen im Bereich der Wasseraufbereitung, z. B. zur Entfernung von Schwermetallionen-Schadstoffen wie Blei, Cadmium und Quecksilber aus Grundwasser, Industrieabwässern und kommunalen Abwässern. Die hochgradig kontrollierbaren Porengrößen und die Oberflächenfunktionalisierung von MOF-Filmen ermöglichen eine effiziente Adsorption und selektive Abtrennung bestimmter Schwermetallionen. Sie spielen auch eine Rolle bei der Adsorptionsbehandlung und Rückgewinnung für Umweltsanierungs- und Abwasserbehandlungsprozesse. MOF-Filme können bei der Adsorption von Schwermetallionen eine effiziente Abscheidung und Rückgewinnung der Zielmetalle ermöglichen. Durch geeignete Nachbehandlungsmethoden können die adsorbierten Schwermetallionen aus dem MOF-Film desorbiert werden, wodurch eine effektive Rückgewinnung und Wiederverwendung von Metallressourcen erreicht wird.
7 Komposit-Filtermembran
Komposit-Filtermembranen unterscheiden sich von herkömmlichen Filtermembranen aus einem einzigen Material dadurch, dass sie zwei oder mehr Materialien kombinieren, um ihre jeweiligen Stärken voll zur Geltung zu bringen und die Defizite des anderen auszugleichen, wodurch eine effizientere und zuverlässigere Filtration erreicht wird. Zu diesen Materialien können Polymere, Keramiken, Metalle, Nanomaterialien usw. gehören. Jedes Material hat einzigartige physikalische, chemische und mechanische Eigenschaften und kann je nach den verschiedenen Filtrationsanforderungen flexibel kombiniert werden.
In Lithium-Ionen-Batterien dient eine PVDF-MOF-Verbundmembran mit einer durchgehenden MOF-Schicht als Hochleistungsdiaphragma. Die einheitliche Porenstruktur und die Subnanokanäle mit verbundenen offenen Metallstellen in der kontinuierlichen MOF-Schicht können einen gleichmäßig verteilten Li+-Fluss erzeugen, die Bildung dendritischer Vorsprünge verhindern und die elektrochemische Leistung verbessern.
Abb. 11 PVDF-MOF-Verbundseparator mit kontinuierlicher MOF-Schicht [5]
Im Bereich der Meerwasserentsalzung hat sich die Membrandestillation (MD) als eine alternative Strategie zur Meerwasserentsalzung herauskristallisiert, mit der die Kapitalkosten und der Energieverbrauch erheblich gesenkt werden können. Beim MD-Verfahren werden fast 100 % der nichtflüchtigen Bestandteile entfernt, und es gibt keine Beschränkung der Speisewasserkonzentration, während das druckgetriebene Umkehrosmoseverfahren (RO) weniger Potenzial für die Behandlung von Lösungen mit hohem Salzgehalt und geringer Wasserrückgewinnung hat. Die flüchtigen Bestandteile werden mit Hilfe einer mikroporösen hydrophoben Membran aus dem Zulaufgemisch abgetrennt, und das System arbeitet unterhalb des Siedepunkts der Zulaufflüssigkeit. Für MD-Anwendungen werden häufig polymere Materialien mit niedriger Oberflächenenergie, hoher thermischer Stabilität, chemischer Beständigkeit und Inertheit bevorzugt. Polytetrafluorethylen (PTFE) und Polyvinylidenfluorid (PVDF) gelten aufgrund ihrer hohen thermischen Stabilität und Hydrophobie als die wichtigsten kommerziell erhältlichen Membranmaterialien für die Vakuum-Membrandestillation (VMD). PVDF und PTFE sind die optimalen Polymere für VMD-Anwendungen aufgrund ihrer hervorragenden chemischen Beständigkeit und Haltbarkeit. Dank dieser Eigenschaften widersteht PVDF den aggressiven chemischen Umgebungen, die in VMD-Systemen häufig anzutreffen sind, und gewährleistet eine langfristige Betriebssicherheit. PTFE wiederum spielt mit seinen Antihafteigenschaften und seiner hervorragenden Beständigkeit gegen hohe Temperaturen eine Schlüsselrolle. In VMD-Anlagen trägt PTFE zur Verbesserung der Membranleistung bei und verhindert effektiv das Fouling, wodurch ein ungehinderter und effizienter Dampftransport durch die Membran während der Destillation gewährleistet wird. Bei VMD-Anwendungen verbessert die synergetische Verwendung von PVDF und PTFE die Haltbarkeit, chemische Beständigkeit und Betriebseffizienz des gesamten Membransystems.
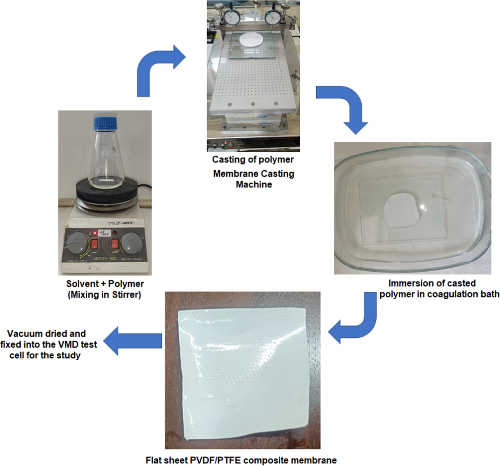
Abb. 12 Flussdiagramm zur Herstellung einer mikroporösen PVDF-PTFE-Verbundmembran [6]
8 Schlussfolgerung
Filtermembranen aus verschiedenen Materialien werden aufgrund ihrer unterschiedlichen Eigenschaften in verschiedenen Bereichen eingesetzt und können je nach den verschiedenen Bedürfnissen zusätzlich zum grundlegenden Filtrationsprozess ausgewählt werden. PVDF-Membranen können zur Filtration von Mikroorganismen wie Bakterien und auch zur Materialreinigung in der chemischen Produktion eingesetzt werden; Keramikmembranen werden meist in der Lebensmittelindustrie zur Abtrennung von alkoholischen Getränken verwendet; Titandioxid-Nanoröhrchen-Membranen können aufgrund ihrer photokatalytischen Eigenschaften für verwandte Anwendungen und die Behandlung von Schwermetallionen eingesetzt werden; Graphenoxidmembranen können für die Molekulartrennung sowie für die Entsalzung von Meerwasser und die Trennung von Öl und Wasser verwendet werden; Kohlenstoffnanoröhren können als Umkehrosmosemembranen eingesetzt werden; und MOF-Membranen können aufgrund der Art der Koordinationsverbindungen zur selektiven Trennung von Schwermetallionen verwendet werden. Darüber hinaus können je nach den Erfordernissen der verschiedenen Anwendungsszenarien verschiedene Arten von Filtrationsmembranen zusammen verwendet werden, und der zusammengesetzte Membrantyp kann eine bessere Filtrationswirkung erzielen, indem er die Eigenschaften der verschiedenen Arten von Filtrationsmembranen aus verschiedenen Materialien ergänzt.
Stanford Advanced Materials (SAM) kann nicht nur eine breite Palette von Filtrationsmembranprodukten anbieten, sondern auch eine professionelle Auswahlberatung, die Sie
sofort in Anspruch nehmen können.
Weiterführende Lektüre:
Referenzen:
[1] Khayet M ,Feng C ,Khulbe K , et al. Preparation and characterization of polyvinylidene fluoride hollow fiber membranes for ultrafiltration[J]. Polymer,2002,43(14).
[2] Li M ,Cheng S ,Zhang J , et al. Verbundmembranen auf Poly(vinylidenfluorid)-Basis mit kontinuierlicher metallorganischer Gerüstschicht für Hochleistungsseparatoren von Lithium-Ionen-Batterien[J]. Chemical Engineering Journal, 2024, 487.
[3] Hu W, Zhang F, Tan X, et al. Herstellung von antibakteriellen PVDF-Verbundfilmen mit korallenartiger hierarchischer Struktur für Selbstreinigung und Strahlungskühlung[J]. ACS Applied Materials & Interfaces, 2024.
[4] Wei Y ,Li K ,Li P , et al. Enhanced ceramic membranes filtration by PS pre-Oxidation with CuO assisted FeSO4 catalytic for NOM removal in drinking water treatment[J]. Separation and Purification Technology, 2024, 345.
[5] Keramische Membranen und ihre Anwendung in der Lebensmittel- und Getränkeindustrie[J]. Filtrieren und Trennen, 2000, 37(3).
[6] Mala M M ,S. S ,S. F , et al. Meer- und Brackwasserentsalzung durch eine neuartige hydrophobe PVDF-PTFE-Verbundmembran durch Vakuum-Membrandestillation[J]. Discover Chemical Engineering,2024,4(1).